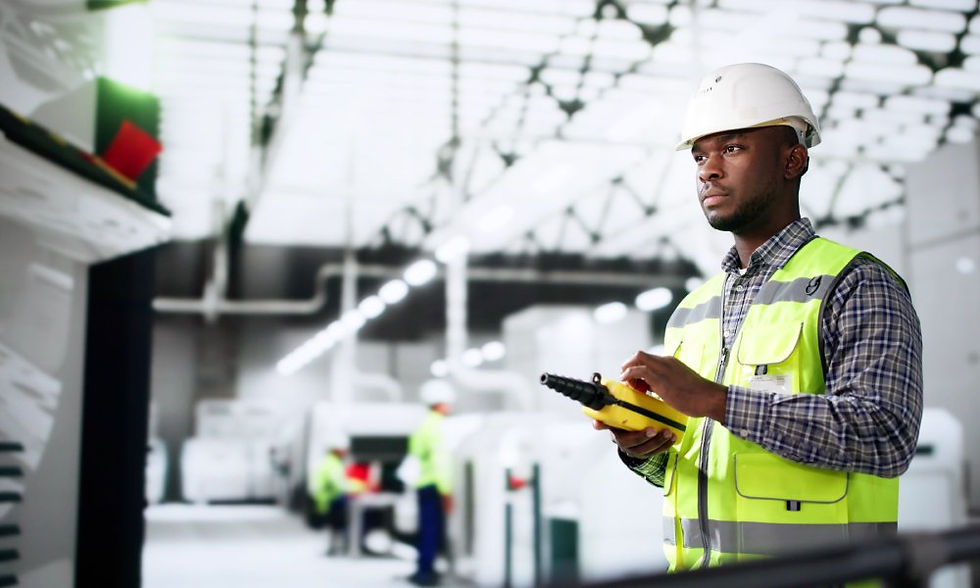
As a business owner, finding ways to curtail expenses while ensuring smooth operations is paramount. Maintenance costs, if you’ve left them unchecked, can quickly escalate and erode your profits. Thankfully, there is a world of ways that you can lower maintenance costs at your business. A little bit of work in the right places can go a long way toward saving your business money and making maintenance easy. Here are some tips.
Regularly Inspect and Maintain Equipment
Regular inspections and maintenance of your equipment are essential for identifying potential problems early. By addressing issues promptly, you can prevent costly repairs or replacements. Make it a habit to schedule routine maintenance checks for all equipment, using diagnostic tools to assess its condition.
Also, keep detailed records of any work done, including replaced parts and service dates, to track equipment performance over time. Implementing a comprehensive maintenance checklist can streamline this process and help you make sure that you’re not overlooking anything important.
Use the Right Equipment and Materials
Using high-quality equipment and materials may require a larger upfront investment but can save you money over time. Cheaper options might seem cost-effective initially, but they often lack durability and are prone to frequent breakdowns, leading to higher maintenance costs.
For example, if you use storage tanks, it’s important that you also invest in tank liners to reduce the maintenance, repairs, and replacements that you’ll do over time. Polymer-based tank liners have numerous benefits, and when you invest in similar high-quality equipment and materials, you can capitalize on these benefits.
Maintenance will never go away. However, when you invest in your equipment instead of cutting corners, maintenance can be easy and save you money in the long run.
Train Your Employees
Properly trained employees are crucial for reducing maintenance costs. They should not only be knowledgeable about using equipment correctly but also adept at identifying warning signs of potential issues and following proper maintenance procedures.
Invest in comprehensive employee training programs that cover equipment operation, basic troubleshooting techniques, and safety protocols. These programs can save you money in the long run by teaching workers how to avoid costly accidents. Additionally, training improves overall workplace safety and efficiency.
Keep a Clean and Organized Workspace
A clean and organized workspace not only boosts productivity but also reduces maintenance costs. Cluttered workspaces can obscure potential hazards and allow contaminants to damage equipment over time.
Implement a regular cleaning schedule and encourage employees to maintain tidy work areas by providing clear guidelines and responsibilities. Moreover, provide the necessary tools and cleaning supplies to facilitate proper maintenance and cleanliness.
Lowering maintenance costs at your business requires proactive and continuous effort. However, investing in proper maintenance now can save you from costly repairs and replacements in the future, ultimately enhancing your business’s overall financial health and efficiency. Use these tips to build a more financially stable future for your business today!
Comments